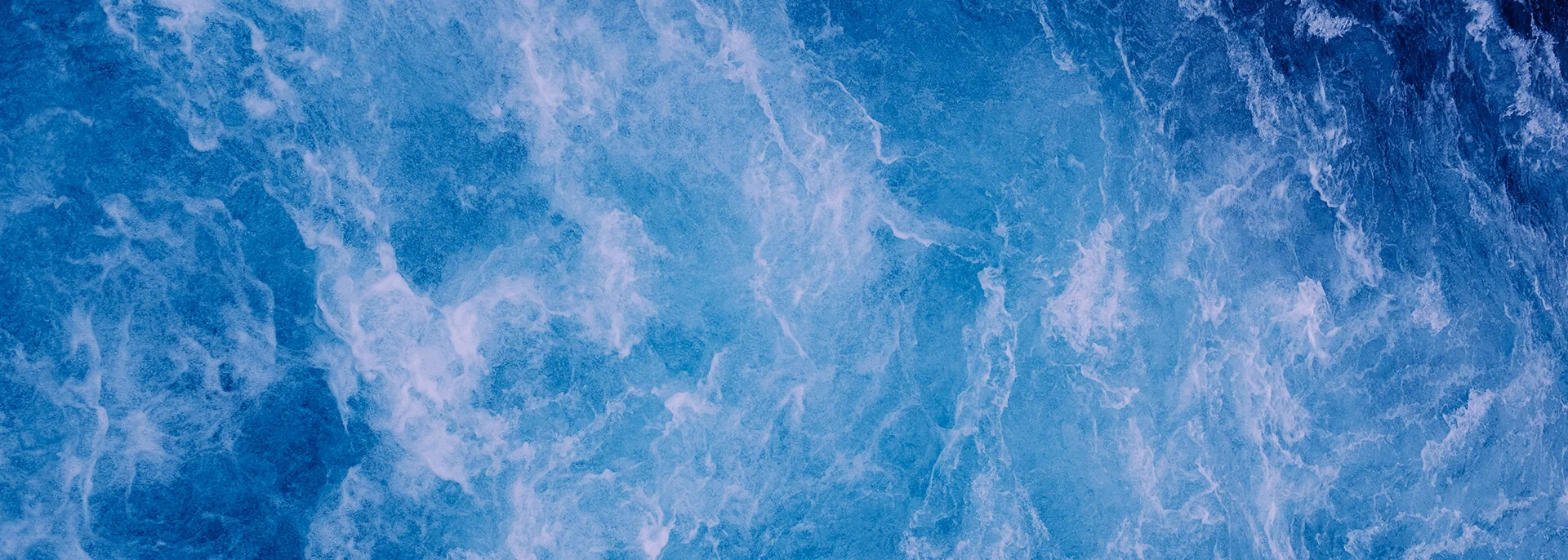
NEWS
FEBRUARY 12, 2019
EUREKA RESOURCES IS ISSUED SECOND PATENT BY THE UNITED STATES PATENT OFFICE – “METHOD AND SYSTEM FOR TREATING WASTEWATER”
The second patent issued to Eureka by the USPO represents the full dewasting-level treatment and resource recovery process that Eureka has engineered and optimized, and currently has in full-scale operation.
FIELD OF THE INVENTION
The present invention relates to methods and systems for processing wastewater. More specifically, the present invention relates to processing wastewater, such as that generated when recovering oil and natural gas, to produce a de-wasted water (water that is no longer considered a residual waste and can be stored in fresh water impoundments) product meeting or exceeding beneficial use criteria, such as the required properties of General Permit WMGR123 (Pennsylvania Department of Environmental Protection, 2012). Further, the present invention relates to producing dry sodium chloride (salt), lithium carbonate and liquid calcium chloride (approximately 20% or approximately 35%) from processed wastewater for beneficial use.
BACKGROUND OF THE INVENTION
Extracting oil and natural gas from unconventional resources, such as shale gas formations, through the combination of horizontal drilling and hydraulic fracturing has increased at a rapid pace in recent years. The Marcellus Shale and Utica Shale are sedimentary formations that underlie most of Pennsylvania and West Virginia and extend into parts of Virginia, Maryland, New York and Ohio. These shale formations are two of several important gas reserves in the United States and together they are one of the largest natural gas “plays” in the world. A “play” is the geographic area underlain by a gas or oil containing geologic formation.
Development of these gas plays and other unconventional resources presents significant potential for economic development and energy independence, but also presents the potential for environmental impacts on land, water and air. For example, between 10% and 40% of the water used for hydro-fracturing a gas well typically returns to the surface as flowback, or later as produced water. In addition to fracturing fluids added by drillers, this wastewater picks up other contaminants from deep in the Earth.
In some parts of the United States, gas drilling companies typically dispose of wastewater deep in the ground, by using Class II injection wells. However, the geology in some locations, such as in Pennsylvania, does not necessarily allow for deep injections. Although municipal treatment plants previously accepted this wastewater, certain states, such as Pennsylvania, prevent publicly owned wastewater treatment facilities (POTWs) from accepting water that has flowed back after fracturing without a certain level of pretreatment. This restriction is thought to promote the goal of establishing and maintaining a closed loop process for the recycling and reuse of oil and gas liquid wastes. States other than Pennsylvania also restrict the ability of publicly-owned treatment works to accept oil and gas wastewaters.
Recently, a number of states have passed regulations to treat processed wastewater having specific properties as a non-waste product. For example, General Permit WMGR123 (Pennsylvania Department of Environmental Protection, 2012) identifies specific water quality criteria that, if met, will not require wastewater after it is processed to be treated as waste. The specific criteria of Appendix A of WMGR123 are reproduced below in Table 1.
TABLE I General Permit WMGR123, Appendix A Criteria Property Limits Aluminum 0.2 mg/L Ammonia 2 mg/L Arsenic 10μg/L Barium 2 mg/L Benzene 0.12 μg/L Beryllium 4 μg/L Boron 1.6 mg/L Bromide 0.1 mg/L Butoxyethanol 0.7 mg/LCadmium 0.16 μg/L Chloride 25 mg/L COD 15 mg/L Chromium 10 μg/L Copper 5 μg/L Ethylene Glycol 13 μg/L Gross Alpha15 pCi/L Gross Beta 1,000 pCi/L Iron 0.3 mg/L Lead 1.3 μg/L Magnesium 10 mg/L Manganese 0.2 mg/L MBAS (Surfactants)0.5 mg/L Methanol 3.5 mg/L Molybdenum 0.21 mg/L Nickel 30 μg/L Nitrite- Nitrate Nitrogen 2 mg/L Oil & Grease ND pH6.5-8.5 SU Radium-226 + Radium-228 5 pCi/L Selenium 4.6 μg/L Silver 1.2 μg/L Sodium 25 mg/L Strontium 4.2 mg/L Sulfate25 mg/L Toluene 0.33 mg/L TDS 500 mg/L TSS 45 mg/L Uranium 30 μg/L Zinc 65 μg/L
Accordingly, it is important that public health and the environment are protected as unconventional resource extraction and production activities become a more prominent component of the oil and gas sector. To this end, regulations governing the management of such wastewater have been evolving at the state level, resulting in increased waste management costs for the petroleum industry. Moreover, strict treatment target requirements specified in each state for unrestricted-use water are particularly challenging to meet. In addition, the federal government has also proposed restrictions on receipt of produced waters by POTWs. Aside from the challenges that may be posed by the regulatory levels for certain contaminants, de-wasting wastewaters from oil and natural gas production pose other challenges, including but not limited to the large fluctuation in daily flow rate of the wastewater; the variation in total dissolved solids (TDS) levels; and variable concentrations of emulsified oil and methanol.
There is therefore a need in the art for methods and systems and for processing oil and gas wastewater with a goal to reuse the processed water, such as for water used in well fracturing while recovering/generating useable byproducts. It would be especially beneficial if such wastewater could be processed to produce both by-products for beneficial use as well as de-wasted water, i.e. unrestricted-use water that is not classified as a residual waste. The production of marketable by-products would reduce the costs of treatment. The production of de-wasted water would allow for less burdensome storage, transportation, and reuse or the potential direct discharge of the water keeping it in the hydrologic cycle.
SUMMARY OF THE INVENTION
One embodiment of the invention is a method for treating wastewater. The method includes the steps of receiving a wastewater, screening the wastewater to determine the optimal treatment approach, pretreating the wastewater to an acceptable quality for thermal mechanical crystallization/evaporation, preheating a portion of the wastewater, feeding the wastewater into an evaporator circulation loop, passing the wastewater through a heating chest, forming NaCl crystals in an evaporation/crystallization unit, circulating smaller NaCl crystals back to the evaporator circulation loop, and separating larger NaCl crystals out of the evaporation/crystallization unit. The embodiment may be configured such that the heating chest is part of the evaporator circulation loop. The embodiment may also include a step of washing the NaCl crystals with a condensate to generate a substantially pure NaCl. The substantially pure NaCl may be at least 98% pure. The NaCl crystals may be dewatered using a centrifuge or like device.
The embodiment may also include routing centrate/filtrate remaining after the larger NaCl crystals have been separated back to the evaporation/crystallization unit. The centrate/filtrate may be mixed with a portion of the wastewater as it is fed to the evaporation/crystallization unit. Vapor from the evaporation/crystallization unit may be passed through a demister and/or other mechanical device to remove water droplets. The vapor may be compressed after the water droplets have been removed. The compressed vapor may be used to heat the wastewater. Condensate from the process may be used for sealing water and wash water.
The embodiment may also include a screening step to determine if the wastewater has high concentrations of methanol, high concentrations of oil, or low concentrations of total dissolved solids. Once screened, methanol can be removed from wastewater with high concentrations of methanol, total dissolved solids can be concentrated in the wastewater that has low concentrations of total dissolved solids, and oil can be removed from the wastewater with high concentrations of oil. Wastewater high in methanol may be processed in a rectification column, wherein the bottom product from the rectification column is passed to a thermal mechanical distillation/evaporation unit and the methanol from the rectification column is stored in a methanol storage tank. The total dissolved solids can be concentrated using a thermal mechanical distillation/evaporation unit. The oil from wastewater high in oil can be removed by first mixing the wastewater high in oil with an emulsion breaking chemical. Once mixed, the wastewater/emulsion mixture is passed through a centrifuge to break the mixture. Once broken the mixture is allowed separate in a separation tank. The mixture may also be heated to assist in separating the oil from the wastewater.
Wastewater from the evaporation/crystallization unit may comprise a condensate/distilled water and a concentrated mixed brine solution/mother liquor comprising approximately 18 to 20% CaCl2) purge. The condensate/distilled water may be made suitable for unrestricted reuse in the oil and gas industry, discharge to surface water under an NPDES permit, or reuse in the treatment process.
The concentrated brine from the evaporation/crystallization unit may be passed to a cooling tank, where it is available for reuse or further treatment in a second stage thermal mechanical evaporation/crystallization unit to generate a high purity 35% CaCl2).
Another embodiment may by a system for treating wastewater that includes a wastewater input line for receiving and segregating wastewater for treatment, a system for pretreating wastewater to an acceptable quality for thermal mechanical crystallization/evaporation, a heat exchanger configured to preheat a portion of the pretreated wastewater, an evaporation/crystallization unit configured to receive and evaporate pretreated wastewater, a heating chest, a circulation line configured to recirculate pretreated wastewater from the evaporation/crystallization unit, through the heating chest, and back into the evaporation/crystallization unit, an NaCl washer connected to the evaporation/crystallization unit and configured to spray pretreated wastewater into a settling area of the evaporation/crystallization unit to wash NaCl crystals from the evaporation/crystallization unit, and a centrifuge configured to receive NaCl crystals removed from the evaporation/crystallization unit by the NaCl washer and dewater the NaCl crystals.
The system may also include a demister or other mechanical devices configured to receive vapor from the evaporation/crystallization unit and remove water droplets from the vapor. The system may also include a compression unit configured to receive the vapor from the demister and/or other mechanical devices. The compression unit may include blowers, compressors, or blowers and compressors. The system may also include a circulation route configured to route the vapor from the compression unit to a heat exchanger. In some embodiments, a sealing water holding tank configured to receive the vapor from the compression unit. The system may also include an input for receiving steam from an external source.
The system may also include a system for routing wastewater to a general wastewater stream, a low total dissolved solids stream, a high methanol stream, a high oil content stream, and a high solid materials stream. The low total dissolved solids stream includes a thermal mechanical distillation/evaporation unit configured to receive wastewater low in total dissolved solids and a distillation/evaporation unit output line for receiving distilled water. The high methanol stream includes a rectification column configured to receive wastewater high in methanol and a rectification output line connected to the rectification column for receiving methanol from the rectification column. The high methanol stream may also include a bottom product line connected to the rectification column for receiving wastewater with less methanol than the wastewater high in methanol, and a distillation/evaporation unit connected to the bottom product line for receiving wastewater with less methanol than the wastewater high in methanol. The high methanol stream may also include a distillation/evaporation unit positioned up-stream of the methanol rectification column, wherein the distillation/evaporation unit removes suspended solids from the wastewater. The high oil content stream includes a high oil stream line for receiving the wastewater with a high oil content, a centrifuge for emulsion breaking, a gravity separation tank for receiving an oil water mixture from the centrifuge, and a heated separation tank connected to the gravity separation tank.
Another embodiment may be a method for treating CaCl2) including the steps of receiving a fluid comprising approximately 20% CaCl2), recovering lithium carbonate from the fluid, and processing the fluid through a second stage thermal mechanical evaporation/crystallization unit, wherein the second stage thermal mechanical evaporation/crystallization unit is configured to generate high purity approximately 35% CaCl2), distilled water and a mixed brine reject stream.